導入事例3
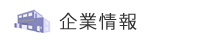
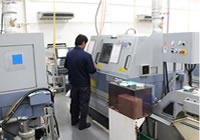
営業品目 | 金属精密切削加工 研磨加工 組み付け、組立 |
所在地 | 静岡県牧之原市 |
従業員 | 25名 |
導入前
- メールとFAXで受注を受取り、初工程の作業者が材料注文書と移動現品票を発行していました。
- 品質管理のため移動現品票に加工ロットと良品数・不良数を記入(実績集計なし)していました。
- 材料は、使用量や残材がつかめず、材料在庫の精度が低い状況でした。
問題点
- 材料在庫の精度が低い、棚卸しても合わない
- 生産指示が現場まかせ、在庫や生産ロットや安全在庫を考慮した生産ができない
- ロット管理を手で行っている
- 社内作業の負荷把握ができず、日程調整が難しい
- 業務手順を改善したいが、糸口が見つからない
- 原価把握したいが、確認できない
- 問題点の改善効果が把握できず、改善に時間がかかる
改善ポイント
製品の構成と工程を登録することで、材料費、購入費、外注費、社内費に分けて標準原価の分析ができるようになりました。
内示受注データと確定受注データを生産管理システムに取込み、材料と加工の手配を行い、検収・在庫・納期など生産管理を実現しました。
導入効果
- 材料所要量計算をもとに注文書作成、使用量を実績入力、在庫精度が改善しました。
- 受注残と在庫数・発注残の照合で必要数計算、生産計画の精度が向上しました。
- 購入指示と検収実績を対比、数量も納期も予定と実績を管理できました。
- 材料から加工、出荷までのロット管理を行い、ロット追跡が簡単にできるようになりました。
- 部署別に仕事量を把握でき、作業前に日程調整や改善対策を実施できました。
- 標準原価計算したマスターをもとに日次決算しますので誤差が改善糸口となりました。
- 改善効果は製品別に確認できるため、着目する改善を短時間で対策できる様になりました。